Loading Up For Pulley Success
Published in Australian Mining
Fenner Conveyors demonstrates the value of testing pulleys at run-conditions prior to site installation, saving a Bowen Basin coal mine potentially millions in part replacement and downtime.
Conveyor systems are a cornerstone of the mining process chain. Within a conveyor system, pulleys are critical pieces of equipment, driving the conveyor belt and enabling change of belt direction.
When equipment fails and a conveyor stops, millions of tonnes of product come to a standstill. That translates to lost productivity and an astronomical financial cost to operators.
This exact issue could have been the fate of a coal mine in Queensland’s Bowen Basin if Fenner Conveyors and its conveyor engineering division, Australian Conveyor Engineering (ACE), had not been contacted to perform load testing of pulleys prior to installation on site.
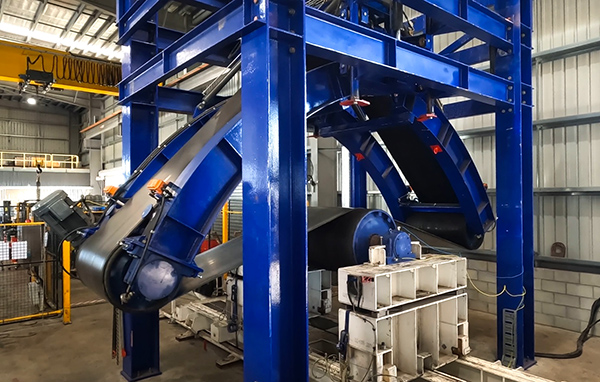
The mine wanted to ensure the quality of (non-ACE) conveyor pulleys before installing in underground operations and contacted its long-time supplier, Fenner Conveyors, for help.
With a network of manufacturing and service locations across Australia, Fenner Conveyors was well positioned to rise to the challenge quickly and efficiently.
ACE was engaged to perform pulley load-testing services, using local, in-house equipment designed to meet the needs of any site.
“Our load-testing machine can be customised to simulate any conveyor condition, giving us a highly accurate report on the pulley performance, revealing any faults before the pulley even gets to site,” ACE engineering operations manager Dean Bazley told Australian Mining.
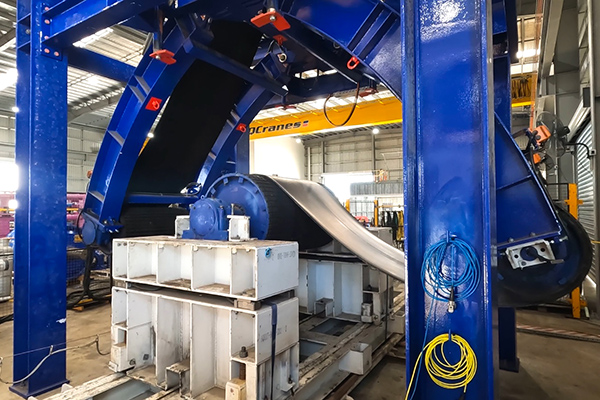
ACE’s load-testing machine also comes with real-time condition-monitoring thanks to the company’s partner, SKF, allowing for instant reportage of even the slightest issue.
Bazley said that of the 16 pulleys ACE analysed with its load-testing machine, six failed to hold up against vibration due to issues such as bearing faults.
“Had the mine site’s pulleys failed on the conveyor and needed replacing, the cost per pulley would be extremely high given the difficult conditions of underground mining, not to mention substantial lost production due to downtime,” Bazley said. “That’s where our load-testing machine really proved its value.”
ACE has been bringing pulley solutions to the Australian mining industry for more than 20 years. But since joining the Fenner Conveyors Group in 2012, both businesses combined forces to become a one-stop shop for the sector’s conveyor needs.
By doing more than completing the load testing for the customer and replacing the unfit pulleys with ACE engineered alternatives, ACE general manager Mark Wilcock emphasised Fenner Conveyors and ACE’s combined ability to deliver complete conveyor solutions to its customers.
“Since the beginning, Fenner Conveyors has developed a strong relationship with the mine site through supplying all their conveyor belting,” he said.
“And today, we’re extending that relationship to include mechanical and electrical engineering and product overhaul supply that realise the benefits of our one supplier offering.”
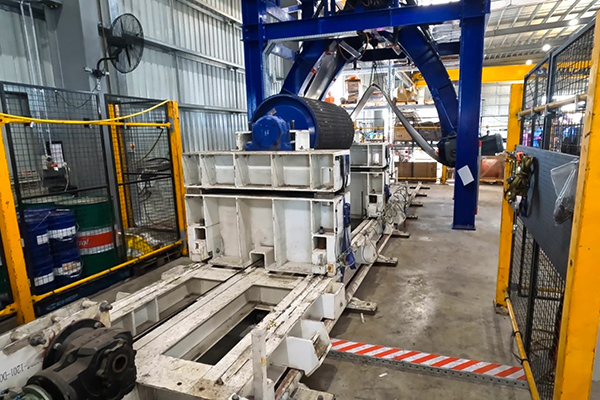
Wilcock said the customer has been extremely satisfied with the commitment of the Fenner Conveyors Group, which has seen savings materialise beyond the site.
“We’re the only player on the east coast of Australia with this kind of pulley testing capability, meaning mines have a highly-valuable solution in their backyard, eliminating the need to ship pulleys across the country for testing where they might be out of action for weeks,” he said.
“Having pulleys travel over thousands of kilometres of road also has the potential to add bearing damage and shorten the life of the pulley, meaning more downtime and lost production.”
While the Fenner Conveyors Group offers a load-testing service for its competitors’ pulleys, Wilcock said the best way to ensure maximum quality is to rely on Fenner Conveyors’ Australian-made pulley offering from the outset.
“Our pulley quality assurance is unmatched,” he said. “We have stringent processes in place to eliminate faults, such as building our pulleys in a cleanroom environment and wrapping the pulleys in UV-stabilised protection to guard against any conditions.
“It’s all about ensuring our customers’ operations keep running smoothly with instant access to conveyor engineering support when they need it.”